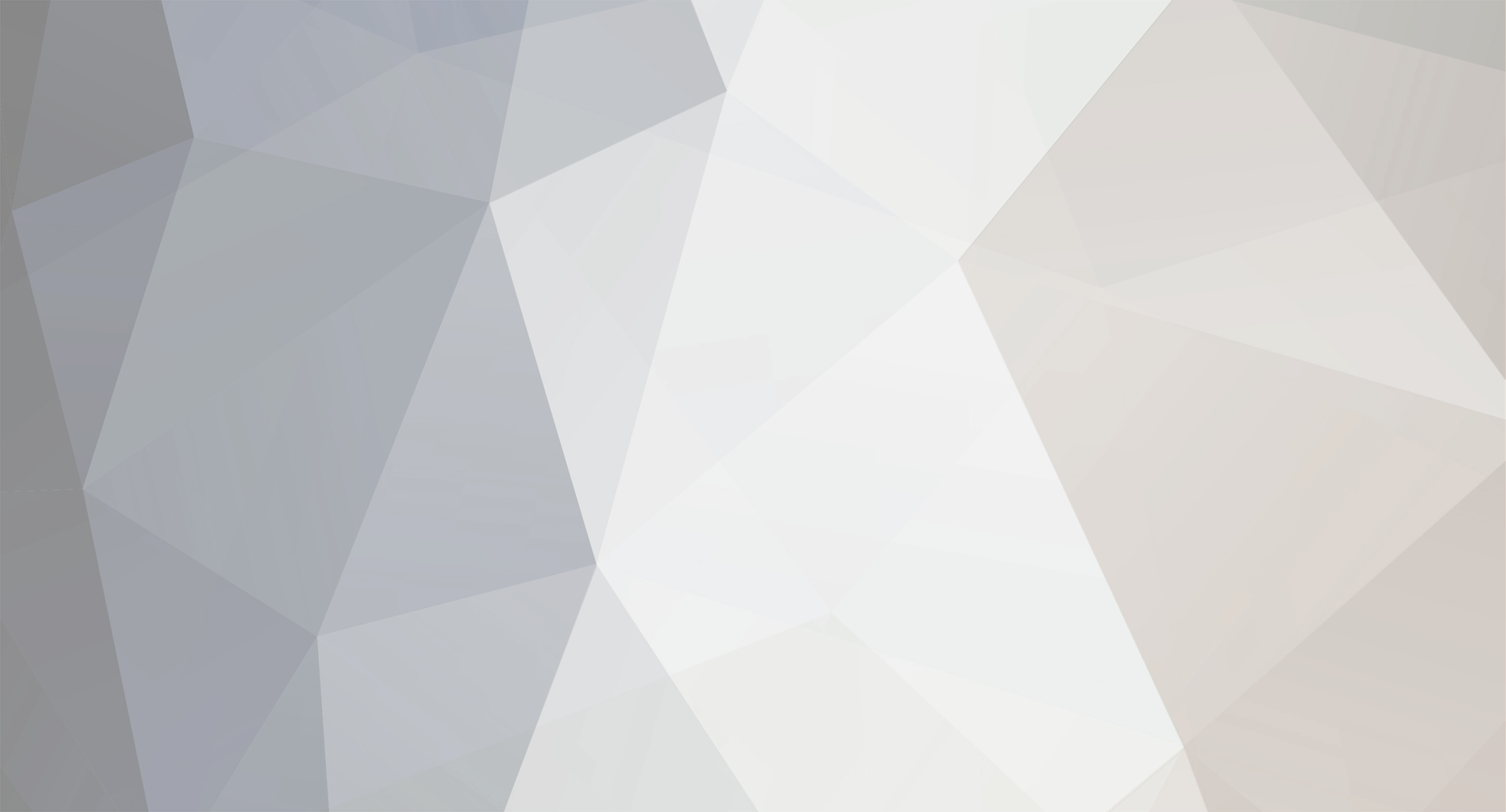
Falcata
Members-
Posts
107 -
Joined
-
Last visited
Recent Profile Visitors
The recent visitors block is disabled and is not being shown to other users.
Falcata's Achievements

Z Dedicated (3/7)
452
Reputation
-
Hi everyone sorry for the delay , everything is ok , just have been super busy helping another car buddy . I have done a couple of renderings thought you might like to see them. There not perfect , just learning how to do them .......... as usual . Once the doors are finished and the hood , I will do them again . it's great to see roughly what it will look like shinny !!! Stay tuned there will be some updates soon. Cheers
-
Hi everyone It's been a year !!!! holy cow the time flies by . It's been crazy here with a harsh winter and moving the workshop , not to mention all the home repairs etc . Well I am happy to let you know I will be back on the build some time next week so stay tuned for updates !!!! Also working on a YouTube Channel to fallow the progress , the first part will be from the beginning and will be in a slideshow format . So looking forward to diving back in !!! Cheers Phil
-
Hi I have some time at the moment better do this now . I was totally stressed out , had to move at a moments notice , a full workshop and the car ...... all the storage places were full or too expensive , just to put the car in was $500.00 a month then to put the rest of the stuff would be another $500.00 a month , and even move if it was on the ground floor where you could drive up to it !!!! . Another Car builder friend of mine was using his brothers car hauler to house his next project the Lambo until his storage container arrived . If the container haden't been delayed I wouldn't have found the trailer . It was a great bit of luck , as there is a shortage of enclosed car haulers here new or used . So with the trailer full of stuff and my Nissan pickup in it it costs $100.00 dollars a month to store it all. So the Lambo belongs to my friend Don who just finished a 308 build . Had a BMW M70 V12 and a Porsche 915 gearbox to go in it , we all talked him out of that !!!. So now he is going LS3 or LS2 So much less hassel and almost double the power . The Deck or balcony I am standing on needs to be replaced , 25 years old and water has gotten in so it's not happy ( been on the list scince before starting the Falcata ) and before the Falcata came it was what I call DNR which stands for Dump N Run I had no time to put stuff away . this is before three truckloads in my little truck arrived from the other shop !!!! And two loads to the dump . So scince the move I have rebuilt the deck and fixed a few cars and done some maintenace on the house . Still a @*!# load of stuff to sort , re arrange etc
-
Hi everyone I know everyone wants to know whats happening with the build . Well as you know I was having an issue with the fiberglass shop in the forest , well the owner kept jerking me around and changing her mind , I just could'nt stand the anxiety an longer , she agreed to the middle of july and a week to move after that . That was just enough time to finish the nose and take molds off the front and back . so i arranged to have a couple of mates come and help to accomplish this . Then june 1st she said she wanted me out in two weeks . so this made me furious !!! So I was forced to purchase a 28 ft enclosed trailer to store my Nissan pickup and a @*!# load of stuff to make room to take the car to my home shop . I will post so pics of the Falcata out side tomorrow !!! I have to go at the moment Cheers
-
Ok Now with a beverage I can continue on . Laying out grid lines on the fenders to make templates like I did on the rear quarters , using the lasers and the center jig I made a while back to keep the tops of the fenders level and even with each other Here are the lines Ok this is the only way I could figure out how to measure the edge of the fenders. I tried going off the front hub but if the steering isn't dead straight would be way off . My Dad who sadly passed away was a brilliant man , him and I built this laser , it's for pointing up , so if you were installing something like lights or ducts , speakers etc. on a ceiling , you would do your layout on the floor and then put the self leveling laser on the mark on the floor and it projects where to put your mark on the ceiling . It has a gimbal bearing to stay level and a center point at the bottom to line up with your marks. it's made from a piece of aluminum tube and some thick aluminum round stock and a laser . i didn't have anything to go off to mark the floor , so I placed the 3 foot rulers on the center of the arch in the centering jig on the car , found the edge of the fender with the laser and read the ruler to check and make sure they were the same , the passenger side was out too far by 1/8th of an inch , remedied by the sander . Ok so now the width is sort of sorted , lets start matching up the rest , yes you guessed it !!! it template and sanding and foaming , and as usual as careful as I try to be , there is always something that needs attention . More grid lines here i was 1/8 tall in this section so I had to sand into the foam and some of the fiberglass fender arch this is the only way I know how to get the same shape on both sides , if anyone know a better way please let me know asap . added some filler over the exposed foam , it's very tricky , you have to sand it before it gets hard or it tears out the foam , it's a real fine line between wet and hard . the pursuit of symmetry .......... I built this adjustable jig to measure off of it really helps but it all so labor intense . So I measure off the center line on the upper tube at the key points mark everything on tape on the tube with a T Square , and then compare each side and fix accordingly . I made a wooden template of this so I could use it repeatedly to fix the other side Here is the foam I had to add from my eager sand way back when . I use everything I can to help me , I have a drawer in the tool box full of paper and cardboard and wood patterns . this is so hard to see what's going on sometimes , too low too tall too deep ahhhhh That explains the beverages , should have built a lambo could have just used plywood lol and yes you have to improvise sometimes , I hope my wife doesn't see her missing knife on here lol Thanks again everyone for fallowing my build and the great comments , the kind words it really helps to keep going on the frustrating days , been a long haul Hope to have the nose sorted and a couple of layers of glass on it so I can bodywork it in the next couple of days , looking forward to seeing the front in primer . Cheers Stay Safe and Stay Tuned in !!!
-
Hi everyone Back with another update , been working on the nose and front fenders Well it's been a long time since I worked on the nose , I remember when I poured the foam in the big cardboard moat , so eager to start carving the foam !!!! So I carved freehand got it close by eye , tape measure and some bits of paper , well that was stupid . Should have built some wooden bucks for a guide , it turned out to be not too bad but still , I had gone too far on the passenger side by 1/2 an inch ( 13 mil ) so have been fixing stuff all week and trying to get it the same as possible to the Drivers side . I was going to make the fenders separate and a center nose piece , but time in the shop in the forest is coming to an end and the plans have changed a bit . I am going to make the front mold all one piece , then make one part from the mold and then cut it and make them separate later . It will make it easier to ship and if you get hit by some bad driver you can just swap out the fender instead of the whole front . So to do that I have to fill in the funky grooves in the center piece with two part foam. Next is to fix the aero bar foam in the center bottom , will take way too long to fix that mess on the car , so I cut it out and made new parts from the foam sheets . it's pretty nasty , and I am too old to lay on the floor and do bodywork . So this is it cut out yup nasty .... getting the angle So this will be way better ,I can router the soft edge for the fiberglass and glue the parts in and glass them with less bodywork . I made a piece for the back with some 1/4 inch foam and then a 3/8 backing to keep it stiff for the glass, Using old wood paneling for the pattern. Here I cut the back edge off the bottom part to allow the back piece room to get glued on to the base . More to come , need to take a small break ( glass of wine or some tequila ) Came home a bit early to start servicing the JapCad ( G35X it's my winter car hasn't run since the end of feb ) My sister is coming for a visit from Toronto soon and would like to use it . Stay tuned for more tonight or in the morning . Cheers
-
Hi everyone last update on the trunk lid bottom plug . This is always fun an a bit nerve racking getting the part out !!! Starting out with a thin flat pry bar it get under the edge , then put wedges in all around where you can the danger here is breaking something on the car by prying or breaking the part , if it's a finished part coming out that is gel-coated you don't want to scratch it with tools such as screwdrivers . I found this little gem at the tool shop on day in the line waiting to check out , it goes flatter than a piece of regular cardboard and you inflate it , it's very strong , I bought the smallest one to try it out , next time I am there I will get another one for sure . here you see it under the part , it's great because it's not sharp and can press on a larger area . I took a couple of videos and will try to put them on . got it off the car ok , now to clean it up , trim the edges and wash the remaining PVA off , it's great stuff also it washes off with water . still need to sand the edges As you can see the carnage from the temp setup to make the part the back the front with the pocket for space for the hinges test fitting looks great !! It still needs to be bodyworked and then make the proper mold for the part , so the finished part has the finished side on the out side , fiberglass is such a lot of work , you need to make three things to get one . 1 the plug 2 the mold 3 the part but once you have the mold you can make lots of them . you see here there is clearance for the part to fit in . Next will be jumping onto the roof , although I feel like jumping off the roof sometimes lol lol this is the part I started to make a while back too attach the roof scoop , not too sure if I like it , it's going to be a bugger to glass and mold , been thinking of a better way . While I was sitting thinking about the roof I got out the masking tape and laid some on the side of the car to get an idea of it filled in . Wow Can't wait !!! to do the doors now ...... Enjoy !! Stay Safe and Stay Tuned In !! Cheers Phil
-
-
Hi everyone as you know I am losing the fiberglass shop soon , not sure exactly when , I am going to ask for an extension to get the molds done on the big parts , like the whole back and front of the cat before having to move it . Ok enough of that depressing thought . Alright a while back I had to change part of the trunk area , i thought it was too tight a curve and might be a problem or a weak spot in the trunk lid , it's a bit confusing even for me lol so I will try to explain as it goes along . So now I have to remake the part that goes to the back of the car ,from where I cut it off . This is this going to be the new plug for the new bottom of the trunk ( boot ) lid ( I have to temporarily fill in the slots for the wing ) Ok you see the part on top of the yellow tape around the trunk opening , well that from the original one I made . But where it turns at the bottom it was too tight and I didn't like it , it got too thin in ths area and i was afraid it would break . So I made the turns softer right where you see it cut off . I glued in a piece of wood and just taped over it next is to simulate the back outside edge of the trunk lid with the piece I made earlier for this reason . Here I glued 2 pieces of 3/16 ths together to mark the edge ( couldn't use a square because it's on an angle ) This get cut off , as it represents the gap for the bottom of the lid to make clearance next is the foam core to make the bottom , now this was cut for the previous version , so it will need to be modified these are spacers to support the foam core underneath , and will give clearance for the rain water escape , they get glued down temporarily Hear you see the back piece is set back so the inside face will become the finished face , I know confusing .... next is gluing a piece of foam core to the top of the back edge to make the bottom flange to bond to the bottom of the top part of the lid . it gets taped to seal the edge of foam core , and you can see I am making some patterns to add foam core to the large base cover where I changed the corners . the black line represents the edge of the base cover , so I need to fiberglass this area to match the top part around the opening . Here I am adding some thin aluminum flashing to the upper part to run the fiberglass on , this will allow extra space for an even thickness later when making the part . ( I know I don't have a pic crazy ) you will see when its back on the car . the bottom side this line shows me how thick the fiberglass needs to be to form the proper gap checking to make sure it level and figuring out a pocket for the Hinge to go in . flashing to make the form extensions for the back sides they have little dams where the new piece needs to terminate these will get waxed so it will release after . a few layers of glass here i remove the end dam and the turned up part will get trimmed off to match the top trimmed and the RHS test fitting the foam core base before adding to corners that nee to be altered here you see the flashing on the upper part , which now get temp glued to hold for glassing . making the addons for the foam core . testing the addons it's good so the base gets held down temporarily with 2 sided tape ,can't fasten from the top , no access after it glassed to remove it from the car when it\s lined up and ready just press down evenly only one shot at it !!! next is to add the foam block which will be the pocket for the hinge I am kind of cheating here , normally you would glass over this and bodywork it etc before glassing , but I am under the gun to get everything glassed now that can't be done off the car , because of the move and it will be easier to bodywork from the other side and off the car . so I am just taping the foam and the edge seams , kind of an experiment , hope it works !!!! what could go wrong lol next is a few coats of wax and spray with PVA mold release cut all the material before getting sticky a few coats of PVA and we are ready to glass stage one Ok looking good , on to stage two some stiffeners to keep the base in place and firm for body working the other side , going to make them out of foam with a 45 degree edge that's easy for the glass to go over if I tape them back to back I can bevel them in the router table a quick sand and they are ready next is to lay them out and glue them down next is to prep some material and glass them Well I am happy with how it turned out , I know its probably a little boring but its all part of it . This morning I will pop it off the car and trim the edges thanks again for all the comments and support , would have loved to do a YouTube series on the build but I would have needed someone to shoot the vids and help produce it it takes about 3 hours a day , unfortunately I just don't have the time , maybe I will do one on installing the body on the car , let me know what you think . Cheers Phil
-
Hi it will be mostly white with red , Black and silver graphics , I have the livery in my mind but I am not talented enough to do a rendition sorry , I would love it though . Thanks for fallowing along . Cheers Phil
-
Hi don't worry about thinking a bout a negative comment , I have had a few on my350z.com , at least you took the time to post your thoughts , yes I would have liked to have the Exhaust tip be lower also . The reasons for it being where it is are , 1st the perfect place is where the factory bumper is and I don't want to mess with the safety features of the car by moving the bumper up or down , the only safe modification to me was to extended the bumper brackets to allow room for the exhaust pipes to go behind it . 2 there wasn't really enough room below the bumper for the exhaust tip without it being susceptible to curb damage or making the tip and mounting brackets any more complicated than they are already . 3 I didn't want the signature exhaust tip to be lost down in the weeds lol , more in your face and the license plates don't deserve the focal point . Thanks for your interest and comments I hope this helps answer why. Cheers Phil
-
Hi everyone , it's time for another quick update . I decided to prime the rear bumper yesterday , there was a brief gap in the weather to spray it outside , it wasn't 100 % perfect but I was dyeing to see it in one color . I went for it and only got one coat of high build on it before it started to sprinkle rain . But I must say I am very please with the look and the lines . Like I said it's not perfect just yet , still a few spots to touch up and the bottom edges Thanks for fallowing and the great feed back . Stay Safe and Stay Tuned for more to come !!!
-
Hi everyone had a great day yesterday , got a couple coats of high build primer on the back of the car . Its still wet here It is a high build to take out imperfection's when block sanded You can finally see the shape , I must say I am happy !!! Still wet in this shot , it was almost 7 pm and I was nackered will a couple more pic today with it flashed off . Well off to the shop for more fun !!!! Stay Safe and stay tuned for more Cheers
-
Hi everyone time for another update . And I must thank you for fallowing my build , the feedback is fantastic !! much appreciated . Still on the back of the car .......... I keep slaving away at it , so here's what's been going on. Here I am making a quick tool for sanding the gas filler opening , very hard to keep the reveal correct . one part to keep the top radius in check and one for the bottom I can attach the sand paper to them and try to keep a nice edge guide coat Another quick sanding block to help things , these are very easy to make i use a contour gauge , then trace it and cut it out the radius on the back deck is too large for my liking , so I am building it up with some filler and will router it with a .25 round over bit . Here is a couple of coats of High Build Primer , so good to see some solid color on it , even if it gets sanded off more checking for symmetry ......it's like measuring an egg ........... what a pain tons of work to keep these quarter panels the same ......... the exhaust tip off the car , its hard for me to put the bumper cover on and off by myself with it on more templates I start with them every 8 inches apart to get the main shape the every 4 inches to dial it in . yup tons of work indeed hoping to get the quarters primed today or tomorrow . Thanks again for all the support . Cheers Stay Safe and Stay Tuned In
-
Hi everyone another update . This is called a guide coat , it's for sanding to show you where the low spots are or scratches , you can spray it on , which takes time to dry and some brands clog up the sand paper , I have started using this powder version , it's a graphite and works very well . This is how I get both sides as close as I possible can to match up , after the wooden bucks on the car get filled with foam , they get roughed out with a long sanding board , this tends to make the foam flat between the bucks and you loose some of the curves . So after the foam is close in shape it gets 2 layers of fiberglass mat for a base to add filler without damaging the foam. I did the passenger side firs for the final shaping because the filler cap for the gas is going to be the original from the Zed , so it has to fit properly . Next I lay out some lines on the car to keep a reference , then make templates to transfer the shap to the other side of the car using the laser to ensure the height . they all get numbered and I drill a hole at each end of the level line to transfer the line to the other side of the template . As you can see there is a ton of shape in these quarter panels here on the drivers side you can see it's getting close !!! this is frame #3 passenger side As you can see here the laser line on frame #3 drivers side , the outboard end of the template needs to go down a bit , so some more sanding . Ah too much fun !!! Stay tuned and stay safe !! Cheers